US Robotics Industry: Automation’s Impact on Manufacturing and Logistics
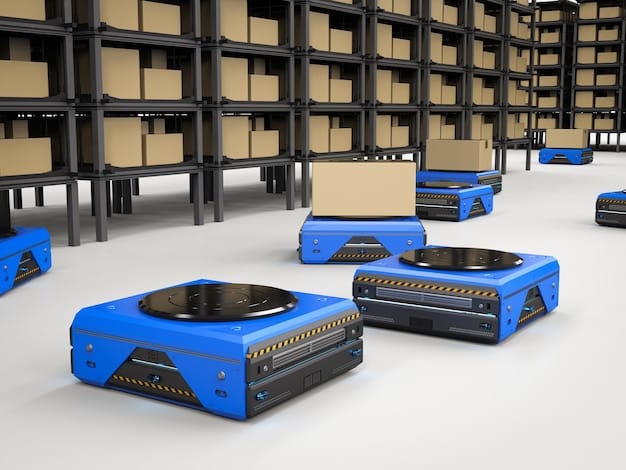
The US robotics industry is revolutionizing manufacturing and logistics by increasing efficiency, reducing costs, and improving safety through automation technologies.
The US robotics industry: How automation is transforming manufacturing and logistics, is undergoing a monumental shift, driven by groundbreaking advancements in robotics and artificial intelligence. This evolution is not merely a technological upgrade; it represents a fundamental change in how goods are produced, distributed, and managed across various sectors. As companies strive for greater efficiency, reduced costs, and enhanced safety, automation is emerging as a critical solution.
The Rise of Robotics in US Manufacturing and Logistics
The **US robotics industry: How automation is transforming manufacturing and logistics**, is experiencing unprecedented growth, fueled by the need for greater productivity and reduced operational costs. The integration of robots into manufacturing and logistics operations is no longer a futuristic concept but a present-day reality, reshaping industries across the United States. From automotive assembly lines to e-commerce fulfillment centers, robots are performing tasks with greater speed, precision, and consistency than ever before.
Key Drivers of Robotics Adoption
Several factors are driving the rapid adoption of robotics in US manufacturing and logistics:
- Labor Shortages: The manufacturing and logistics sectors are facing persistent labor shortages, making it difficult for companies to meet production demands. Robots can fill these gaps by automating tasks that are difficult to staff.
- Cost Reduction: While the initial investment in robotics can be significant, the long-term cost savings are substantial. Robots can operate 24/7 without breaks, reducing labor costs and increasing overall efficiency.
- Improved Safety: Many manufacturing and logistics tasks are hazardous, exposing workers to potential injuries. Robots can perform these tasks safely, reducing the risk of accidents and improving workplace conditions.
- Enhanced Quality: Robots are capable of performing tasks with greater precision and consistency than humans, resulting in higher product quality and reduced defects.
The adoption of robotics is not limited to large corporations. Small and medium-sized enterprises (SMEs) are also increasingly investing in automation technologies to improve their competitiveness. As the cost of robots decreases and their capabilities expand, the barriers to entry are becoming lower, making it easier for companies of all sizes to embrace automation.
The Future of Manufacturing: Automation and Robotics
The future of manufacturing in the US is inextricably linked to automation and robotics. As technology continues to advance, robots will become even more capable and versatile, performing a wider range of tasks with minimal human intervention. This will lead to further increases in productivity, efficiency, and quality, solidifying the US robotics industry’s position as a global leader in manufacturing and logistics.
The Impact of Automation in Manufacturing
The **US robotics industry: How automation is transforming manufacturing and logistics**, has profoundly changed the manufacturing sector, streamlining production processes and enhancing overall efficiency. Automation in manufacturing involves using robots, computer-controlled machines, and other advanced technologies to perform tasks with minimal human intervention. This transformation has resulted in significant improvements in productivity, quality, and safety.
One of the primary benefits of automation in manufacturing is increased productivity. Robots can operate continuously without breaks, performing tasks faster and more accurately than humans. This leads to higher production volumes and reduced lead times.
Specific Applications of Automation in Manufacturing:
- Assembly Line Automation: Robots are used to assemble products with precision and speed, reducing the risk of errors and ensuring consistent quality.
- Welding and Cutting: Automated welding and cutting machines can perform these tasks with greater accuracy and repeatability than manual methods, resulting in stronger and more durable products.
- Painting and Coating: Robots can apply paint and coatings evenly and efficiently, reducing waste and improving the appearance of finished products.
- Material Handling: Automated guided vehicles (AGVs) and autonomous mobile robots (AMRs) are used to transport materials throughout factories, reducing the need for manual labor and improving workflow.
Automation has also improved the quality of manufactured goods. Robots are able to perform tasks with greater precision than humans, reducing the risk of defects and ensuring that products meet stringent quality standards. This leads to higher customer satisfaction and reduced warranty costs.
The automation transforms manufacturing by not only increasing productivity but also improving worker safety. Hazardous tasks, such as lifting heavy objects or working with dangerous chemicals, can be performed by robots, reducing the risk of injuries and illnesses.
Transforming Logistics Through Robotics
The **US robotics industry: How automation is transforming manufacturing and logistics**, is not only impacting manufacturing, but also revolutionizing the logistics sector. Robotics in logistics is transforming warehousing, transportation, and delivery operations, making them more efficient, accurate, and cost-effective.
Warehouses are becoming increasingly automated, with robots performing tasks such as picking, packing, and sorting orders. Automated storage and retrieval systems (AS/RS) can quickly and efficiently retrieve items from storage, reducing the time and labor required to fulfill orders.
Key Applications of Robotics in Logistics:
- Warehouse Automation: Robots are used to automate tasks such as picking, packing, and sorting orders, improving efficiency and reducing labor costs.
- Transportation: Autonomous trucks and delivery vans are being developed to transport goods more efficiently and safely.
- Last-Mile Delivery: Drones and robots are being used to deliver packages directly to customers’ doorsteps, reducing delivery times and improving customer satisfaction.
Robotics is also improving the accuracy of logistics operations. Robots are able to scan and track items with greater precision than humans, reducing the risk of errors and ensuring that orders are fulfilled correctly. This leads to higher customer satisfaction and reduced return rates.
The increased efficiency of logistics operations is directly linked to the use of robotics. Robots can operate 24/7 without breaks, processing orders faster and more accurately than humans.
Challenges and Opportunities in Robotics Adoption
While the benefits of robotics in US manufacturing and logistics are clear, there are also challenges that companies must address in order to successfully adopt these technologies.
One of the biggest challenges is the cost of implementation. Robots and other automation technologies can be expensive, requiring a significant upfront investment. However, companies can mitigate these costs by starting with small-scale automation projects and gradually expanding their use of robotics over time.
Navigating the Challenges include:
The integration of robotics also requires a skilled workforce. Companies must train their employees to operate and maintain robots, or they may need to hire new employees with the necessary skills.
- High initial costs: The initial investment in robots and automation systems can be substantial.
- Integration complexities: Integrating robots into existing manufacturing and logistics processes can be challenging and require careful planning.
- Workforce adaptation: The adoption of robotics may require retraining or upskilling of the existing workforce.
Despite these challenges, the opportunities for robotics adoption in US manufacturing and logistics are enormous. As technology continues to advance and costs decline, more and more companies will be able to take advantage of the benefits of automation.
To harness the opportunities, companies need to develop a clear strategy for robotics adoption, taking into account their specific needs and goals. It is also important to invest in training and education to ensure that employees have the skills necessary to operate and maintain robots.
The Future of Work: Human-Robot Collaboration
As robots become more prevalent in US manufacturing and logistics, the nature of work is changing. Many tasks that were once performed by humans are now being automated, leading to concerns about job displacement.
However, the future of work is not about robots replacing humans entirely, but rather about humans and robots working together. Humans can focus on tasks that require creativity, problem-solving, and critical thinking, while robots can handle repetitive and dangerous tasks.
Strategies for Effective Human-Robot Collaboration
To make this vision a reality, companies need to invest in training and education to help employees develop the skills necessary to work alongside robots. They also need to create a work environment that fosters collaboration and teamwork between humans and robots.
* Skill Development: Focus on training programs that teach employees how to program, operate, and maintain robotic equipment.
* Collaboration Tools: Implement software and communication systems that allow humans and robots to coordinate their work effectively.
* Safety Protocols: Establish clear safety guidelines and procedures to ensure that humans and robots can work together safely.
The successful integration of robots into the workforce will require a shift in mindset, from viewing robots as replacements for humans to seeing them as valuable tools that can enhance human capabilities.
Embracing human-robot collaboration can lead to a more productive and fulfilling work environment, where humans and robots work together to achieve common goals. This will require a commitment to training, education, and collaboration, but the rewards will be well worth the effort.
Policy and Investment in Robotics
Government policies and investments play a crucial role in fostering innovation and adoption in the US robotics industry. Policies that support research and development, incentivize automation, and promote workforce training can accelerate the growth of the industry.
The US government has already taken steps to support robotics, through initiatives such as the National Robotics Initiative, which funds research and development in robotics and automation. However, more can be done to create a supportive environment for robotics adoption.
Government Initiatives and Funding
* Tax Incentives: Offer tax breaks to companies that invest in robotics and automation technologies.
* Research Grants: Increase funding for research and development in robotics and artificial intelligence.
* Workforce Development Programs: Support training programs that prepare workers for jobs in the robotics industry.
In addition to government policies and investments, the private sector also has a role to play in fostering innovation in robotics. Companies should invest in research and development, collaborate with universities and research institutions, and support the development of open-source robotics platforms.
By working together, government and industry can create a vibrant and dynamic robotics ecosystem in the US, driving innovation, creating jobs, and ensuring that the US remains a global leader in manufacturing and logistics.
Key Point | Brief Description |
---|---|
🏭 Automation in Manufacturing | Increases efficiency, quality, and safety in production processes. |
📦 Robotics in Logistics | Transforms warehousing, transportation, and delivery operations. |
🤝 Human-Robot Collaboration | Enhances productivity and fulfillment in workplaces. |
💰 Government Investments | Policy support R&D and workforce training, boosts robotics growth. |
Frequently Asked Questions
What are the main benefits of using robotics in manufacturing?
Increased efficiency, reduced costs and enhanced safety. Robots automate repetitive tasks, ensuring consistency.
How do robots improve logistics and supply chain operations?
Robots automate warehousing, package sorting, and delivery, saving time plus improve efficiency.
What is the role of government in promoting robotics adoption?
Government supports robotics advances, funding R&D and workforce training to spur growth.
What are some challenges to integrating robots in existing facilities?
One challenge that is often unseen is how to train current staff to use the products, so there is high initial cost.
How will human-robot collaboration shape future job roles?
Humans excel in creativity, problem-solving, & critical thinking. Robots will do monotonous & dangerous jobs.
Conclusion
In conclusion, the **US robotics industry: how automation is transforming manufacturing and logistics**, has had a transformative impact on both manufacturing and logistics. As technology continues to evolve, the adoption of robotics will accelerate, creating new opportunities for businesses and workers alike.